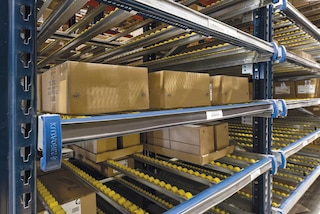
Types d'emballage en logistique : primaire, secondaire, tertiaire
Le type d'emballage d'un produit déterminé a des implications qui vont au-delà de la protection du produit. Outre l'effet de son aspect esthétique sur le client, la taille, le matériau utilisé et le design ont un impact direct sur les coûts liés au stockage et au transport. Les décisions relatives aux choix des emballages primaires, secondaires et tertiaires sont donc de nature hautement stratégique pour l'entreprise.
Dans notre article, nous passons en revue les principaux concepts liés à la sélection de l'emballage des produits d’un point de vue logistique. Quelles différences existe-t-il entre les types d'emballage primaire, secondaire et tertiaire ? Quelles sont les fonctions de chacun d'eux ?
Quels types d'emballage existe-t-il ? Emballage primaire, secondaire et tertiaire
Le conditionnement d'un produit est formé par plusieurs couches d'emballage. Voici leur définition selon la Directive 94/62/CE de l'UE :
- Emballage primaire, emballage de vente ou unité de consommation
L'emballage primaire contient et protège le produit. Il est en contact direct avec l'article qu’il doit maintenir dans des conditions optimales. Cet emballage définit la plus petite unité de consommation et permet la vente unitaire du produit. Nous le retrouvons sous diverses formes : boîtes de conserve, pots, sacs, bouteilles...
Les fonctions de cet emballage primaire sont les suivantes :
- Identifier le produit selon les normes en vigueur et montrer les informations relatives à son utilisation, ainsi que d'autres données fondamentales comme la date de péremption.
- Selon le produit, il doit également remplir le rôle important d'identification de la marque et attirer davantage le consommateur.
- Garantir une position stable dans le rayon de vente du magasin (qu'il ne tombe pas).
- Garantir l’isolement du contenu.
- Protéger le produit avec le minimum de matériau possible.
- Emballage secondaire ou groupé
L'emballage secondaire est un regroupement d'emballages primaires. Il offre une plus grande protection et permet la commercialisation du produit à plus grande échelle. Il s'agit principalement des caisses en carton, bien qu'elles pourraient également être en plastique. Par exemple, dans le cas du lait, un Tetra Brik individuel serait l'emballage ou conditionnement primaire et la caisse en carton qui contient le pack de six représenterait l'emballage secondaire.
Les fonctions de l'emballage secondaire sont les suivantes :
- Résister à l'empilement (dans l'entrepôt et dans le point de vente) et à la manipulation pendant le transport, afin d'éviter que le produit ne subisse de dommages.
- Contenir une quantité déterminée de produits.
- Attirer l'attention du client, plus particulièrement les emballages secondaires destinés directement à la vente au public.
- Emballage tertiaire
Les emballages tertiaires regroupent les emballages primaires et secondaires pour créer une unité de chargement plus importante dont la forme la plus courante est la palette ou le conteneur et les caisses en carton modulaires qui les composent.
Les fonctions et caractéristiques de l'emballage tertiaire sont :
- Être stable et permettre le compactage des charges.
- Exploiter au maximum la capacité de stockage des installations et des véhicules industriels.
- Être homologués et fabriqués avec des matériaux résistants.
- Parfois, l'emballage tertiaire peut également jouer un rôle important en ce qui concerne l'image de marque. Soulignons le cas de la logistique e-commerce, où la caisse ou l'emballage utilisé pour le transport est de type tertiaire et peut inclure des éléments visuels de la marque (citons comme exemple l'emballage très reconnaissable d'Amazon).
Dans ce contexte logistique, il convient de rappeler le rôle de l'unité de charge. Il s'agit de l'unité de base utilisée par l'entreprise dans le transport et le stockage de ses produits. Cela peut être des palettes, des caisses, des conteneurs, des bidons, des bobines, de grands conteneurs pour produits en vrac (IBC ou GRV), des sacs ou des big-bag, etc. Différentes unités de charge peuvent coexister dans une même installation de stockage, elles sont différenciées par zones et avec différents types de rayonnages adaptés à chacune d'entre elles.
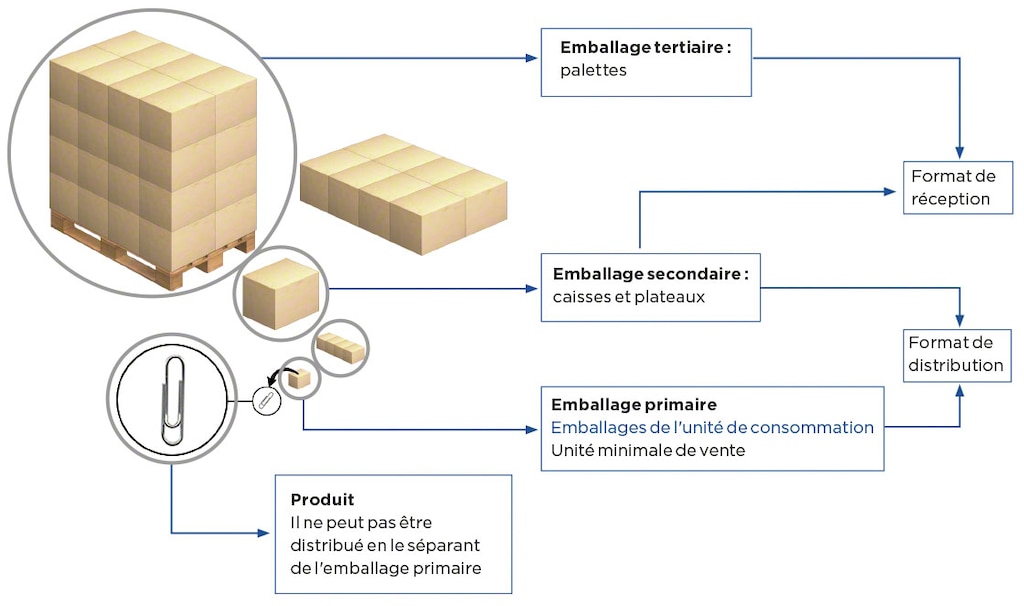
Les facteurs qui déterminent le choix de l'emballage
La sélection du meilleur emballage vise à réduire les coûts directs (achats de matériaux et gestion des déchets) et indirects (processus de packing, manutention, stockage et perte dues à des dommages). Voici les principaux aspects qui conditionnent le choix des différents types d'emballage :
- Les caractéristiques du produit comme, par exemple, son état (liquide, solide, gaz), son poids et son volume, sa fragilité, sa stabilité (s'il se déforme ou s'il reste rigide), s'il est périssable ou non, son degré de dangerosité et sa valeur.
- Le processus de production et d'emballage déterminera le type d'emballages primaires et secondaires à employer. Les formats seront différents en fonction de si l'emballage s'effectue manuellement ou de manière automatique.
- La manutention pendant le transport et le stockage : de nombreux aspects doivent être pris en compte, comme la hauteur d'empilement qu'il doit supporter, la durée de stockage, les différentes méthodes de transport utilisées par l'entreprise (elles peuvent provoquer des vibrations qui affectent le produit), le nombre de chargements et de déchargements qu'il va subir, sa relation avec la logistique inverse (par exemple, certains emballages secondaires sont préparés pour être réutilisés lors de retours e-commerce), ainsi que la température et l'humidité auxquelles va être soumis le produit lors des opérations de stockage et de transport.
- L'impact environnemental des déchets d'emballage et les options de recyclage ou de réutilisation.
- Point de vente : sa place dans le magasin et la manutention dont il va avoir besoin doivent être prises en considération. En outre, s'il s'agit de commerce électronique, il convient de prendre en compte le moment de déballage ou unboxing vu qu’il s'agit du premier contact physique du client avec la marque et son produit.
- Législation et réglementation qui régissent les caractéristiques des emballages comme, par exemple, les normes techniques (des standards tels que l'UNE ou l'ISO), les règlements de transport international (par exemple la Norme internationale pour des mesures phytosanitaires nº 15 ou NIMP-15), la législation liée à l'environnement ou les régulations qui concernent la manutention et le marquage de marchandises dangereuses tel que l'Accord européen relatif au transport international de marchandises dangereuses par route, ADR.
Les stratégies de gestion de l'emballage
Selon le rapport The Empty Space Economy de Forbes Insights, un quart de l'espace de chacun des conteneurs et colis envoyés et reçus par an transporte... de l'air. C'est pourquoi, 66% des responsables interrogés pensent qu'en supprimant cet espace vide, ils peuvent réaliser des économies d'au moins 25% du budget investi dans les emballages.
Certaines des stratégies de gestion des emballages suivantes visent à atteindre cet objectif :
- Standardisation des mesures d'emballage
L'un des principaux avantages de la standardisation des mesures est l'utilisation de l'espace à tous les stades de la Supply Chain, de la production au transport en passant par le stockage. D'où la généralisation de l'utilisation de palette europe comme emballage tertiaire de base pour le compactage des charges dans les pays européens.
Pour qu'une amélioration s'opère, il convient de conclure un accord entre fournisseurs, opérateurs logistiques, distributeurs et points de vente pour choisir des emballages dont les dimensions correspondent à la taille modulaire (multiple d'une europalette) de 600x400mm (1/4 d'une palette europe), 600x800mm (la taille d'une 1/2 palette europe) ou 300x400mm (1/3 d'une palette europe). Cela permet d'optimiser l'empilage des cartons sur les palettes et d'utiliser au maximum l'espace disponible dans les entrepôts et les véhicules de transport.
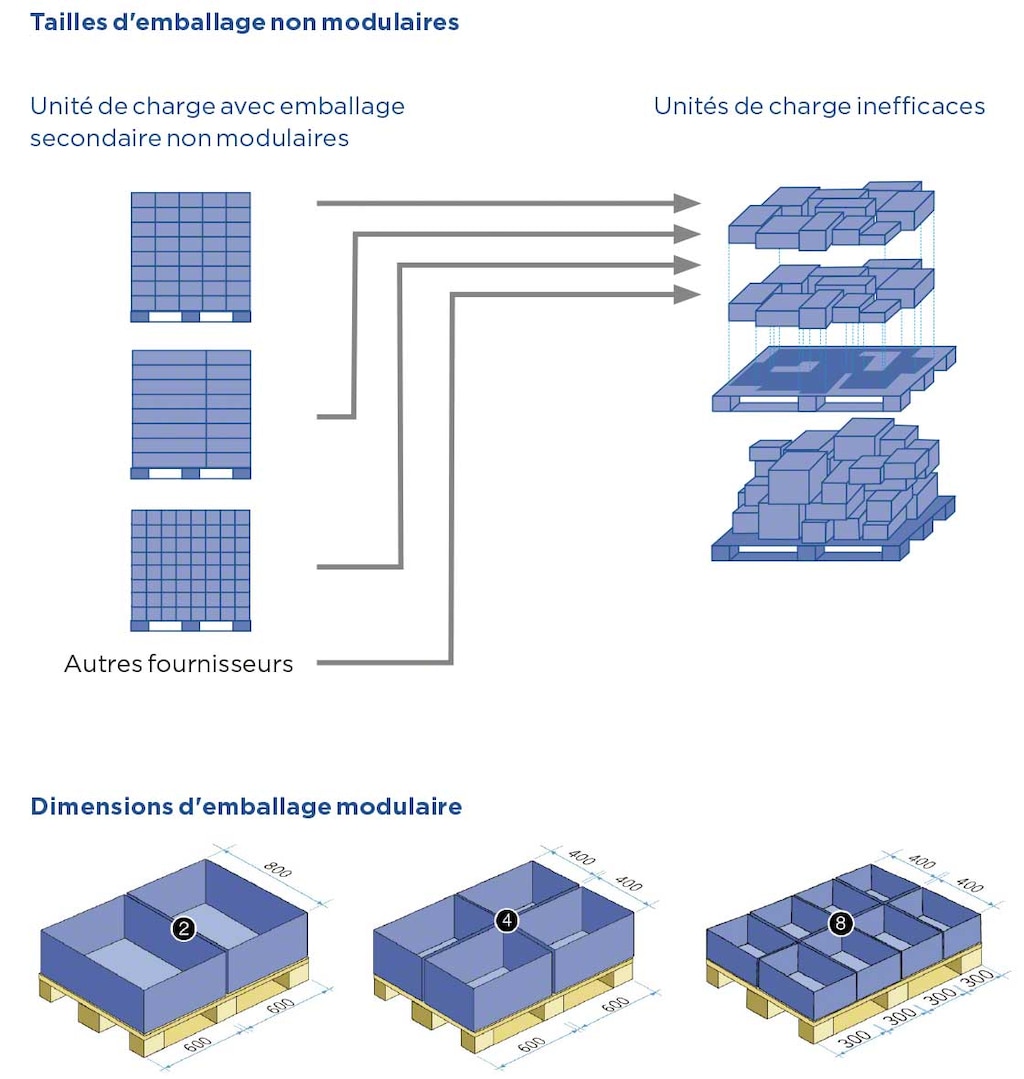
- Automatiser la sélection et la manipulation du matériel d'emballage
Le point de départ consiste à analyser les caractéristiques du stock afin de trouver des mesures de base qui soient modulaires (c'est-à-dire des multiples de la palette europe, comme indiqué ci-dessus) et dans lesquelles s'emboîtent la plupart des produits stockés.
N'oublions pas une variable importante relative aux coûts de transport : le poids volumétrique, c'est-à-dire le calcul de l'espace occupé par une marchandise dans le véhicule par rapport à son poids. Il sert de guide aux agences de transport pour fixer leurs tarifs lorsque les colis sont légers mais volumineux.
Dans ce sens, le système de gestion de l'entrepôt s'intègre avec les PIE (Postes d'inspection d'entrée), les balances, les machines automatiques d'étiquetage et les cobots qui aident lors du processus d'emballage et, sur la base des données de stock, indique à l'opérateur le type d'emballage à utiliser pour préparer chaque commande.
Des emballages pour une logistique plus efficace
Pour identifier les points à améliorer dans la gestion du packaging, il est conseillé de classer les différents types d'emballage primaire, secondaire et tertiaire et d'étudier comment et qui est concerné par une éventuelle modification de chacun d'entre eux.
Dans le domaine de l'industrie, le degré d'optimisation de l'emballage doit être évalué en fonction du matériau dont il est constitué, du transport, de la manutention et du stockage, de la gestion des déchets et du coût qu'il implique. Ce n'est qu'avec une vision globale du processus qu'il sera possible de choisir le type d'emballage logistique le mieux adapté à la réalité de l'entreprise.