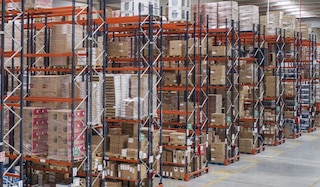
Les 10 problèmes logistiques les plus courants dans un entrepôt
L’évolution continue vers les marchés numériques et les nouvelles exigences des clients a conduit à une augmentation significative des problèmes logistiques, en particulier ceux liés à la gestion des entrepôts.
Mais, quels sont les problèmes logistiques les plus courants ? Dans cet article nous identifions les dix cas les plus courants qui se produisent dans un entrepôt et proposons quelques solutions pour en minimiser les conséquences.
1. Espace inexploité
Le manque d'espace de stockage est l'un des principaux problèmes auxquels la plupart des entreprises sont confrontées. Face à cette situation, qui est principalement causée par une augmentation de l'activité, les entreprises doivent optimiser l’espace de leur entrepôt pour éviter un investissement économique important sur le plan logistique.
L’une des solutions les plus communes pour maximiser l'espace sans modifier la surface est de tirer profit de la hauteur de l’entrepôt en utilisant des rayonnages plus hauts ou des mezzanines et des passerelles. Nous pouvons également optimiser la surface en installant des systèmes de stockage par accumulation, comme le Pallet Shuttle, les rayonnages mobiles Movirack ou les rayonnages par accumulation drive-in.
2. Mauvaise gestion des stocks
Une mauvaise gestion des stocks entraîne des erreurs et des retards lors de la recherche d’un produit, et donc dans les délais de livraison. Un entrepôt bien organisé est la première étape vers la performance logistique.
Pour éviter cela, il est nécessaire d’élaborer une stratégie efficace de répartition de la marchandise qui prend en compte les caractéristiques des références, les systèmes de stockage disponibles, le taux de rotation de la marchandise et les déplacements des opérateurs.
L'utilisation d'un logiciel de gestion d’entrepôt assure le contrôle total du stock de l’entrepôt, en synchronisant les ordres d’entrée et de sortie. Un WMS, par exemple, automatise le processus de répartition des références dans les emplacements de l’entrepôt (slotting) au moyen de critères et de règles préalablement configurés.
3. Erreurs lors du picking
Qu’il s’agisse du mauvais article prélevé ou de plusieurs commandes mélangées, le coût de la logistique inverse (soit les retours d’articles), dus à des erreurs lors de la préparation de commandes, a de graves conséquences sur la logistique d'une entreprise.
Les erreurs lors de la préparation de commandes représentent un surcoût pour l’entreprise. Selon certaines études, son impact moyen est estimé à environ 17 € par commande.
Dans une opération aussi complexe que la préparation de commandes, où les opérateurs produisent généralement plusieurs commandes avec différentes références, l’automatisation est la solution pour supprimer le taux d’erreur et augmenter le nombre de produits collectés par heure dans l’entrepôt.
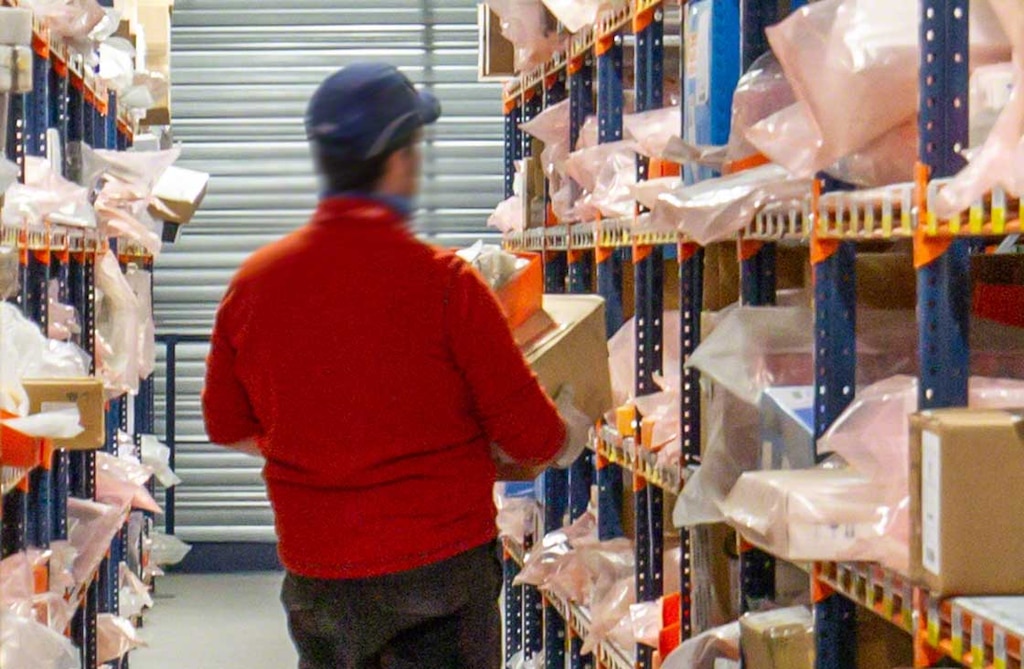
4. Manque de traçabilité
Dans un contexte de chaîne logistique intégrée, les clients et les fournisseurs exigent d’avoir facilement accès aux détails des matières premières composants chaque article et des processus de production et de logistique par lesquels il est passé avant d’arriver entre leurs mains.
La traçabilité d’un produit est l’attribut logistique qui permet d’enregistrer et d’identifier chaque produit d’après son origine jusqu’à sa destination finale, elle est primordiale dans des secteurs comme la pharmaceutique ou l'agroalimentaire. Une erreur de traçabilité peut entraîner des problèmes importants pour les clients, ainsi que pour l'entreprise qui les fournit.
L’implantation d’un logiciel logistique tel qu’un WMS garantit la traçabilité du produit dès son entrée dans l’entrepôt jusqu’à son expédition. Outre cette application, il existe d'autres logiciels sur le marché qui améliorent cet attribut logistique comme la fonctionnalité avancée d’Easy WMS, GPAO pour la gestion de la production. Ce module synchronise le tampon d'approvisionnement avec le tampon de production afin de surveiller le processus de production dans un entrepôt.
5. Inventaire obsolète
Connaître et planifier le stock d’un entrepôt est indispensable afin de maintenir la productivité dans toutes les opérations logistiques. En effet, un entrepôt avec un stock obsolète peut avoir de graves conséquences pour une entreprise, comme des erreurs d’adressage des produits jusqu’à une éventuelle rupture de stock.
A mesure que les entreprises se développent et agrandissent leur catalogue de références, le déploiement d’un logiciel de gestion d’entrepôt devient un outil nécessaire pour connaître à tout moment, la quantité de stock disponible dans l’entrepôt.
6. Erreurs dans la manipulation de la marchandise
La manipulation correcte des unités de charge pour préparer une commande est une des clés pour réduire les erreurs et accroître la productivité. Il faut s’assurer que les opérateurs soient correctement formés, que l’entrepôt dispose d’engins de manutention adaptés et qu’ils soient bien entretenus.
Cependant, l’option qui garantit une manipulation efficace de la marchandise est l’automatisation des systèmes de stockage. Les responsables logistiques optent pour la substitution des engins de manutention habituels, comme les transpalettes et les chariots élévateurs, par des convoyeurs et des transstockeurs, afin d'accélérer le transit des marchandises entre les différents processus logistiques.
Par ailleurs, lors de la manipulation de la marchandise, il est important d’assurer la stabilité des unités de charge, principalement des palettes ou des bacs, pour garantir la stabilité du colis pendant toutes les opérations effectuées dans l’entrepôt.
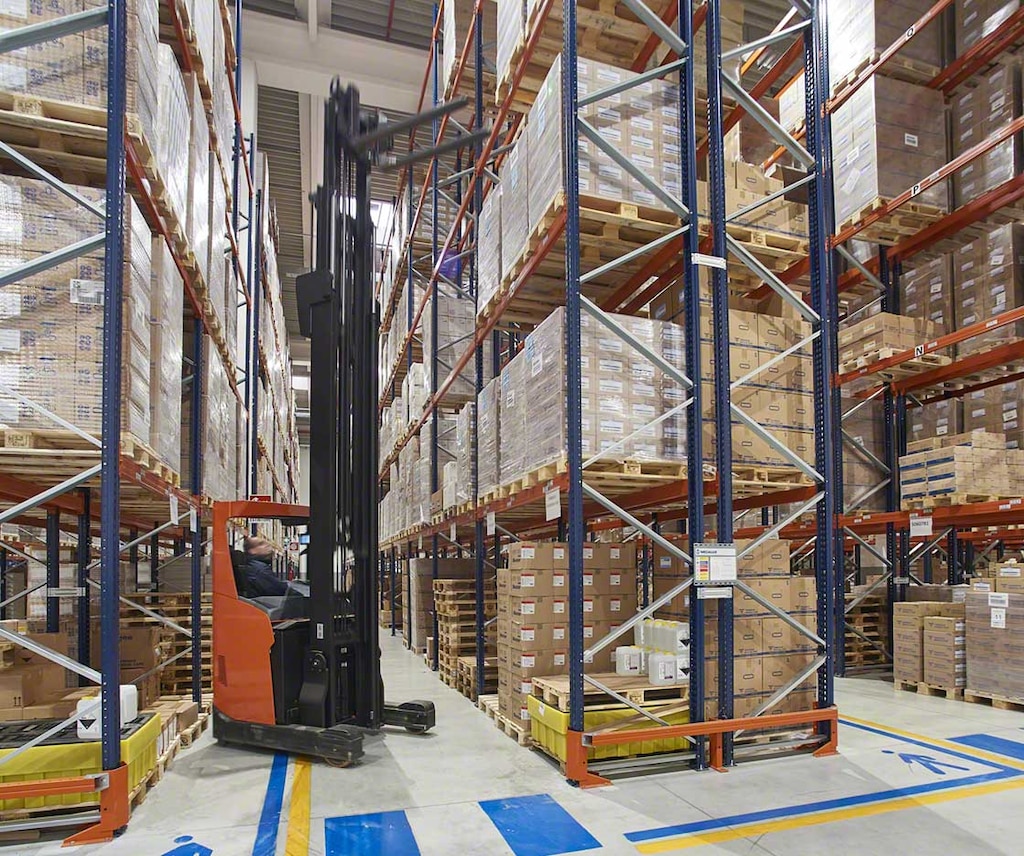
7. Retards dans les expéditions
L’expédition de la marchandise est le dernier processus par lequel passe un produit avant son expédition, soit au client final, soit à un autre centre de distribution ou de production.
Afin que ce processus se déroule avec succès, il est recommandé d’avoir une planification des livraisons à effectuer, de consolider correctement la marchandise, de vérifier scrupuleusement toute la documentation nécessaire pour l’expédition et de charger rapidement et en toute sécurité la marchandise dans le camion.
Un logiciel de gestion d’entrepôt est capable de regrouper les commandes par itinéraire, type de véhicule, client ou selon le niveau de priorité de l’envoi, entre autres.
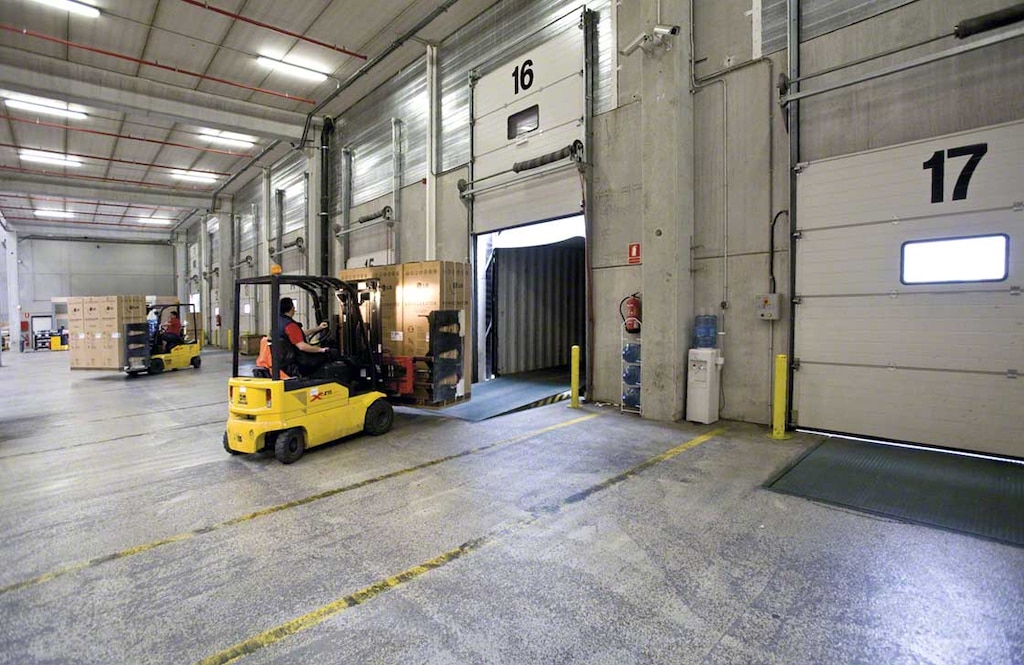
8. Mauvaise signalétique en entrepôt
Dans un espace où coexistent des opérateurs, des marchandises et des engins de manutention, il est obligatoire de mettre en place une signalisation en entrepôt qui minimise le risque d’accident. Les panneaux doivent être placés de manière à être parfaitement visibles au sol et sur les rayonnages, pour qu'ils soient conformes aux mesures de sécurité.
La norme qui impose et régule la signalisation de l’entrepôt est soumise à la Directive 92/58/CEE de l’Union Européenne, qui définit la manière de placer les panneaux dans un entrepôt. Ces signalisations peuvent être de différentes couleurs, symboles et formes, en fonction de leurs caractéristiques et du message à véhiculer.
9. KPI logistiques incorrects
Le meilleur outil pour mener des actions d'amélioration continue dans un entrepôt consiste à utiliser des indicateurs de performance ou KPI logistiques (Key Performance Indicators). Grâce aux données et à la comparaison avec l'historique de l'entreprise, il est possible de surveiller le rendement d'un processus pour en déterminer des axes d'amélioration.
Les KPI logistiques servent à mesurer de nombreux processus qui ont lieu dans un entrepôt : la réception des marchandises, le stockage, la préparation de commandes, la gestion des stocks, les expéditions, les livraisons, le transport et la gestion des retours, par exemple. Si ces indicateurs ne sont pas correctement utilisés ou que les efforts sont concentrés sur l'analyse de KPI incorrects, il sera très difficile d'identifier les évolutions positives ou négatives et d'agir en conséquence afin d'atteindre l'excellence logistique.
Un module comme Supply Chain Analytics surveille toutes les activités de l’entrepôt, calculant les KPI logistiques les plus pertinents pour une analyse ultérieure plus approfondie.
10. L’intégration avec d’autres départements (ERP)
Le responsable d’entrepôt doit se coordonner avec les autres départements de l'entreprise pour atteindre l'objectif final de toute la logistique : que la commande arrive dans les délais et de la manière convenue avec le client.
Pour cela, les différents logiciels de gestion logistique sont intégrés à l’ERP (Enterprise Resourcing Planning), un logiciel regroupant tous ou la plupart des départements d'une entreprise comme, le service comptabilité, le service marketing, le service commercial, etc.
Une mauvaise coordination entre l’entrepôt et le département commercial peut entraîner des erreurs de préparation de commandes ou des commandes incomplètes et donc un impact économique important pour l'entreprise.
Optimisez votre entrepôt
De manière générale, l'automatisation des opérations comme de la gestion d’entrepôt grâce à un WMS, est la meilleure stratégie pour éliminer les erreurs commises et pour un entrepôt plus performant.
Si votre entrepôt est concerné par l’un des problèmes évoqués ci-dessus ou que vous pensez qu’il est temps d’automatiser la gestion de votre centre de distribution ainsi que votre système de stockage, contactez Mecalux. Une équipe d’experts vous aidera à résoudre toute difficulté afin de tirer le meilleur parti de vos processus logistiques.