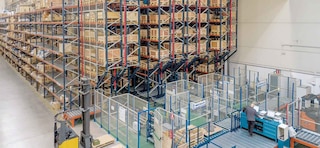
Qu'est-ce que le Lean logistics ? La stratégie de l'efficacité
La méthode du Lean logistics est une philosophie de gestion et d'organisation des opérations d'origine japonaise. Utiliser le Lean logistics consiste à identifier et éliminer les activités qui n'ajoutent pas de valeur à la Supply Chain. Cette technique permet d'augmenter la vitesse des flux de produits et de minimiser les coûts.
Le concept du « Lean » peut se résumer à l’expression « faire plus avec moins », à laquelle nous pourrions rajouter : avec moins d'efforts, moins d'équipements, moins d'espace, moins de coûts et en moins de temps.
Initialement, cet ensemble de techniques s’appliquait au domaine de la production industrielle, d'où le nom de « Lean manufacturing ». Il a été développé par Taiichi Ohno de Toyota.
Les principes de la méthode du Lean logistics
Le Lean logistics vise à réduire les coûts logistiques d’une entreprise en détectant et en traitant les tâches qui n’apportent pas de valeur ajoutée aux processus. Ainsi, la durée du cycle d’une commande est réduite. Il s'agit d'une recherche d'efficacité constante, qu’il est possible de diviser en plusieurs étapes :
1. L’identification des activités avec valeur ajoutée
Grâce à des outils tels que le Value Stream Map, cette première phase met en évidence tous les composants d’un processus en particulier. Dans un entrepôt par exemple, les opérations de préparation de commandes sont divisées en étapes pouvant être décomposées en sous-processus.
2. La détection des sources de perte et leur optimisation
En logistique, les pertes sont souvent liées au temps, comme nous aurons l’occasion de le voir un peu plus loin. La standardisation des tâches et le maintien de la propreté et de l'ordre dans l'entrepôt sont essentiels au bon déroulement de cette phase.
3. La création d’un nouveau flux de processus optimisés
L'objectif est de concevoir une méthode de travail plus efficace en termes de temps et de qualité du service. Pour ce faire, il est nécessaire de supprimer les tâches inutiles identifiées. En plus de réaliser des changements organisationnels, cette phase peut comprendre l'investissement dans de nouvelles technologies ou de nouveaux systèmes qui aident à éliminer les étapes qui prennent trop de temps et n’ajoutent aucune valeur à la Supply Chain.
4. L’utilisation de stratégies dites « pull » pour minimiser les stocks
La gestion des stocks détermine en grande partie la valeur des coûts logistiques. Contrairement aux stratégies « push », qui se basent sur la production selon les prévisions de ventes, les méthodes de production « pull » visent avant tout à attirer les clients et à répondre à la demande en fournissant les produits avec facilité.
5. La standardisation des nouveaux processus sur le long terme
Pour ce faire, il est essentiel d’impliquer et de motiver tous les travailleurs. Ils doivent acquérir de nouvelles habitudes et compétences faisant partie de ce que nous appelons le talent 4.0.
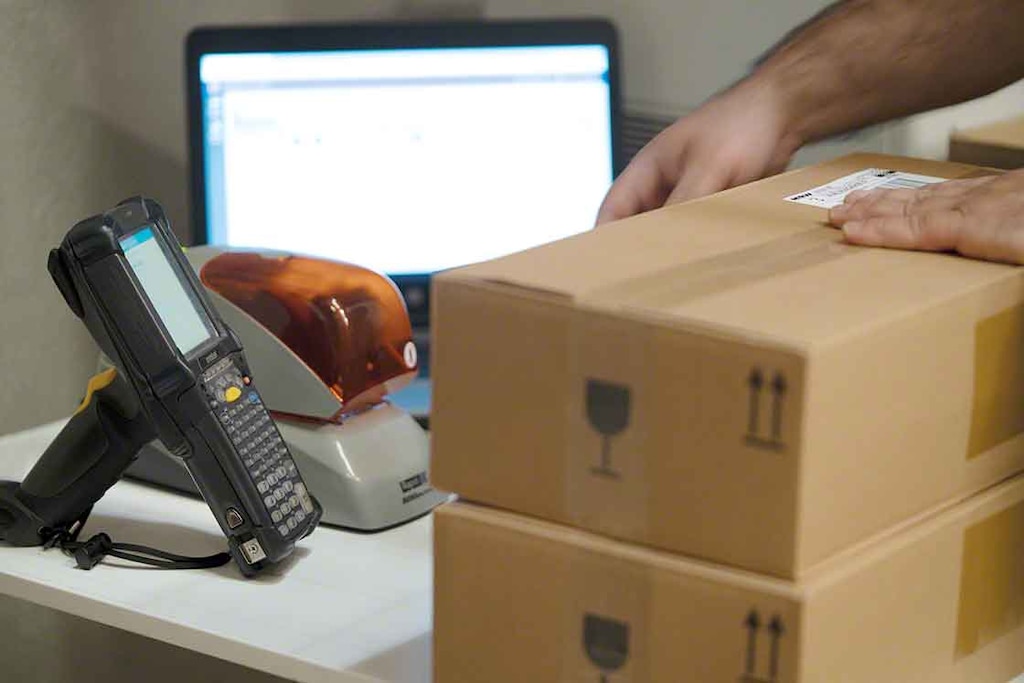
Comment limiter les principales pertes contre lesquelles lutte le Lean logistics ?
Il est possible de classer ces principales pertes en quatre grandes catégories. Examinons en détail leurs caractéristiques et la façon dont elles pourraient être traitées :
- Un excès de marchandises entreposées (surstockage)
Cette augmentation indue des stocks est généralement liée à un excès de production des entreprises manufacturières, mais aussi à une mauvaise prévision des ventes (demand forecasting). Parfois, certaines sociétés augmentent leur stock de sécurité juste « au cas où » ; derrière cette décision, se cache une mauvaise gestion des fournisseurs ou une organisation défaillante des flux de matières.
L’espace de stockage est donc mal utilisé : cela entraîne une augmentation des coûts logistiques et du stockage de produits aux taux de rotation faibles, qui ne sont presque pas renouvelés.
Comment éliminer cette perte d'un point de vue Lean logistics ?
Afin d’appliquer les principes du Lean logistics dans cette situation, il est nécessaire de travailler les facteurs que vous contrôlez (par opposition à d'autres plus éphémères tels que la prévision des ventes). Voici les mesures que vous pourrez adopter dans votre entrepôt :
- L'application de la stratégie de cross-docking qui limite les quantités de stock entreposé au maximum.
- La mise en place de la méthode du juste-à-temps pour gérer les fournisseurs et organiser l'entrepôt.
- La réduction des Lead Times des fournisseurs et des processus intralogistiques. Cela facilite le calcul des prévisions de la demande : ces dernières sont plus précises lorsqu’elles sont effectuées sur le court terme et permettent d'éviter les déséquilibres dus au surstockage.
- Les pertes de temps et les obstacles
Le Lean logistics vise à réduire la différence entre le temps d'exécution (temps de travail pour lequel sont payés vos opérateurs) et le temps standard (le temps de réalisation que vous facturez à vos clients). Le résultat de cette opération se traduira par la découverte des éléments déficients ainsi qu’une réduction des coûts.
Les causes peuvent être très variées et sont généralement liées à une méthode de travail mal conçue, à des incidents contre lesquels aucune mesure n’a été mise en place, ou à une mauvaise répartition de la charge de travail des opérateurs.
Comment résoudre cette perte d'un point de vue Lean logistics ?
- Afin de bien organiser les tâches, d’éviter les obstacles et les pauses, il n’y a rien de mieux que le logiciel de gestion d’entrepôt. Cet outil aide les centres à traiter et organiser d'énormes volumes d'informations tout en donnant la priorité à l'optimisation des processus.
- Mesurer et contrôler la charge de travail de chaque opérateur permet d’éviter que certaines personnes restent les bras croisées pendant que d’autres sont débordées. Le logiciel de gestion de la main-d'oeuvre, application du progiciel Easy WMS est précisément en charge de contrôler cette section.
- Pour éviter que les pannes d'équipement ne ralentissent l'activité de l'entrepôt, il est conseillé de disposer d'un plan d'entretien des engins de manutention et des solutions de stockage automatisé utilisés dans l'entrepôt à titre de mesure préventive, et d'une aide technique pour résoudre les incidents le plus rapidement possible.
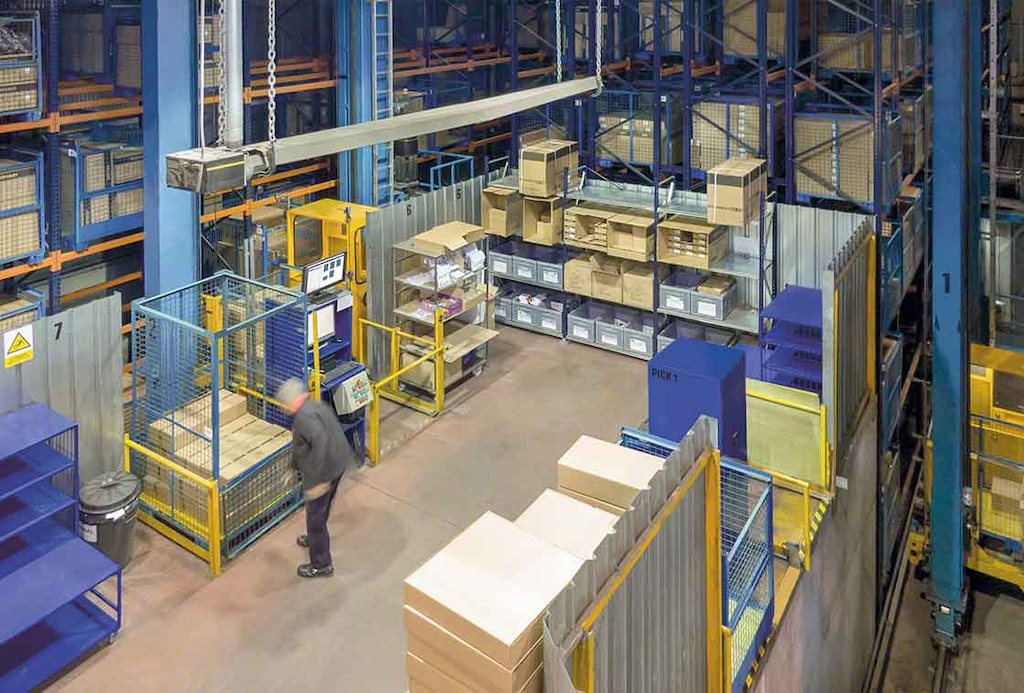
- Les déplacements et mouvements inutiles
Les opérations liées à la préparation de commandes en entrepôt sont celles qui prennent le plus de temps au quotidien. C'est pourquoi, une mauvaise planification des lignes de préparation peut nuire à la productivité de l’entreprise : elle peut se traduire par des déplacements non-nécessaires (exemple : l'utilisation d’engins non chargés), ou par une augmentation des mouvements inutiles.
Comment résoudre cette problématique d'un point de vue Lean logistics ?
- L'automatisation de la manutention des charges est une excellente stratégie pour réduire le temps consacré au transport intralogistique et permet de renforcer la sécurité des opérations. De ce fait, ces déplacements répétitifs sont généralement des processus pour lesquels l'automatisation donne d'excellents résultats. De même, les transstockeurs sont par exemple capables de fonctionner en cycles combinés de manière à ce que tous les mouvements soient utilisés pour porter des charges.
- La méthode de préparation de commandes logistique a également un impact sur le nombre de déplacements effectués. C’est pourquoi, de nombreuses entreprises installent des logiciels WMS : ils facilitent l'organisation des itinéraires de picking dans l’entrepôt en donnant la priorité à la consolidation ou au groupage de marchandises, et ajustent les temps lors de la planification des expéditions.
- Les erreurs responsables des retours clients et des processus répétés
Nous associons généralement un niveau de qualité supérieure à des coûts élevés, et ce même si ceci ne correspond pas toujours à la réalité. En effet, les meilleures entreprises du secteur de la logistique, dont beaucoup appliquent le Lean logistics, offrent un excellent service au juste prix, mais comment font-elles ? Grâce à un élément principal : elles exécutent les opérations correctement dès le premier essai et gagnent ainsi plus d’argent (elles dépendent d’un service exceptionnellement efficace).
Comment y remédier selon une perspective Lean logistics ?
- Si la gestion des retours clients complique les opérations de l'entrepôt, il convient de s’arrêter pour analyser la situation et déduire quelles en sont les causes. Si elles sont les conséquences d’erreurs de préparation de commandes, dans ce cas, notez qu’un WMS comme logiciel de picking peut réduire considérablement ces défaillances et augmenter le niveau global de qualité du service.
- Identifier les incidents à temps est une bonne pratique qui permet d'éviter de travailler deux fois ou de répéter des tâches.
La méthode du Lean logistics, axée sur les économies
Le concept de Lean logistics repose sur le principe que lorsque le client achète un produit, il ne paye pas les activités qui n'ajoutent pas de valeur à la Supply Chain. Cette méthode concentre ses efforts sur l'élimination des éléments inefficaces qui entravent la rentabilité de la logistique de l'entreprise.
Chez Mecalux, nous alignons notre stratégie et travaillons au coude-à-coude avec nos clients pour les aider à atteindre leurs objectifs : nous leur proposons des solutions de stockage automatisé et un logiciel de gestion d’entrepôt à la pointe de la technologie. Contactez nos experts pour qu’ils vous accompagnent sur le chemin du Lean logistics.